Waste Water Not an Option: 5D Technology Helps EchoWater Project Save $400 Million (and a Lot of Water)
Getting Control of the Project
To learn more about the 5D planning, scheduling and costing digital twin that was at the heart of the EchoWater Project and its ability to finish on time and under budget, I interviewed Project Controls Cubed’s Jeff Campbell, director of virtual planning, and Serelle Corn, lead planner and managing member.
Some excerpts from that interview made it into this article, but you can watch the full video interview above or at bit.ly/3Pc4LWB.
Infrastructure “mega projects” have a deservedly bad reputation. Conventional wisdom says they always take much longer than expected and their budgets balloon out of control. Infamous examples of this include Boston’s Big Dig, the “Chunnel” that connects Britain to France and New York City’s Gateway Project railway tunnel. But that doesn’t always have to be the case.
For example, the EchoWater Project in Elk Grove, Calif., is a massive upgrade of an existing wastewater-treatment facility run by the Sacramento Regional County Sanitation District (Regional San), which subesquently merged with and adopted the name of the Sacramento Area Sewer District (SacSewer) on Jan. 1, 2024. It was budgeted to cost $2.1 billion and take 11 years to complete. Unlike the aforementioned mega-project boondoggles, it was completed on time and under budget by $400 million.
The money saved is being reinvested to fund a new project, the Harvest Water Program, that will recycle wastewater to deliver agricultural irrigation water to more than 16,000 acres and potentially raise depleted groundwater by 35 feet. Harvest Water won’t open until 2027, and the cost will be mostly offest due to the savings from EchoWater.
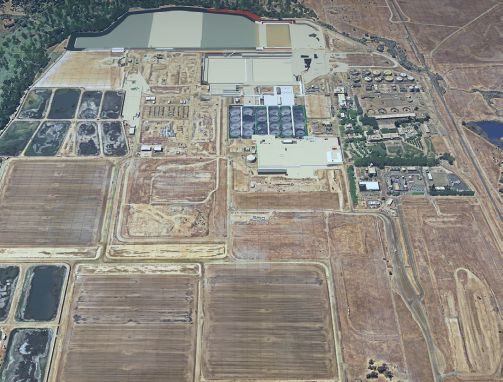
2014
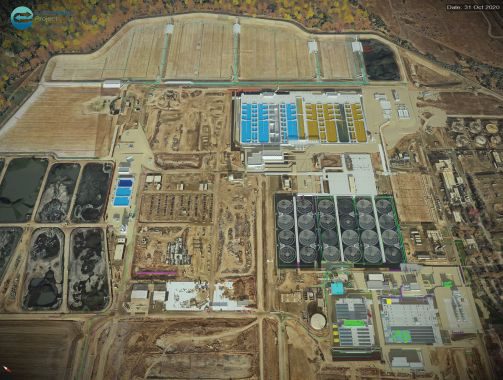
2020
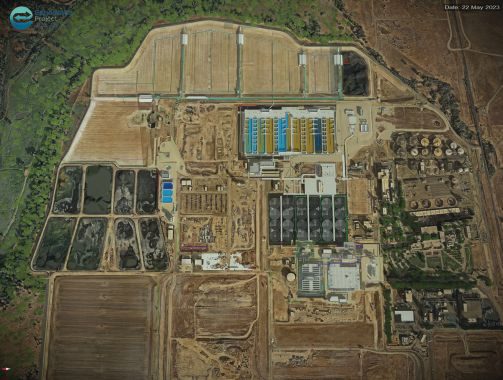
2023
Satellite (top) and aerial photos (bottom) chronicle site development at the EchoWater Project from 2014 to 2022.
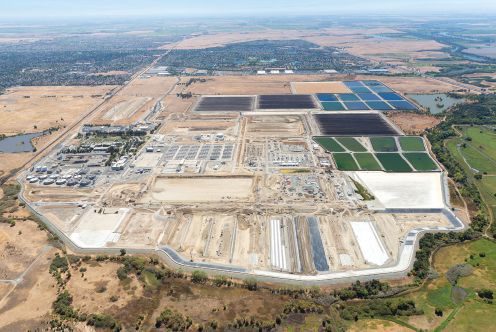
2015
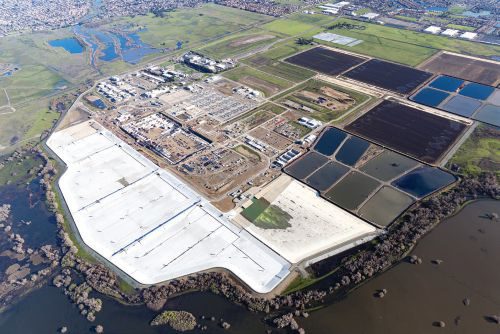
2019
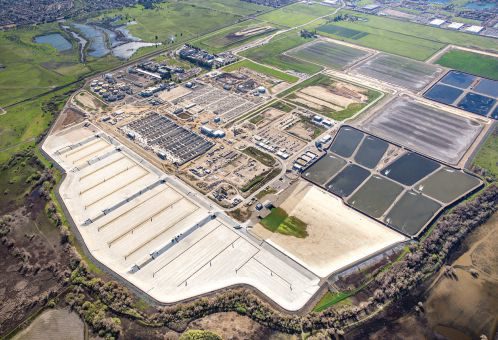
2020

2022
New Requirements Spur Action
SacSewer serves more than 1.6 million people, treating the entire Sacramento region’s wastewater. Its original plant in Elk Grove became operational in 1982 and delivered compliant water throughout its lifecycle.
However, compliance rules changed in 2010 when the Central Valley Regional Water Quality Control Board issued new treatment requirements (upgrading from “secondary” to “tertiary” treatment) in SacSewer’s wastewater discharge permit to improve water quality and help alleviate ecological problems further downstream in the Sacramento River and Delta.
SacSewer tested several possible treatment strategies to achieve the new permit requirements. The approved plan, the EchoWater Project, consisted of 22 individual projects that together used 41,350 tons of steel and more than 225,000 cubic yards of concrete (at the same Elk Grove location). This was a “mega project” by any definition.
The expanded tertiary treatment facility (TTF) now is the second-largest such facility in the nation, treating an average of 135 million gallons of wastewater each day. Its upgraded treatment process now removes 99 percent of ammonia and 89 percent of nitrogen from the wastewater.
Project Controls Cubed
Making the Plan
Vick Kyotani, program manager for SacSewer, was handed supervision of the EchoWater Project in 2012, and he had to achieve compliance by May 2023. “When it was awarded, every engineering construction company wanted this project because it was a really big deal,” explains Jeff Campbell, director of virtual planning at Project Controls Cubed. “It was the very best of the best in the industry going for this program.”
Kyotani awarded the project to the Brown & Caldwell/HDR Joint Venture, which helped establish the EchoWater Program Management Office (PMO). SacSewer then subcontracted a variety of additional design and construction firms, including Black & Veatch, Carollo Engineers, Jacobs and others.
SacSewer already had a computerized maintenance management system (CMMS) running through IBM’s Maximo software, but with so many firms working at the same time in different areas, it was understood early that project management and scheduling would be crucial for success.
To help in this area, the EchoWater PMO signed Project Controls Cubed to the team to manage the project’s planning, scheduling and cost control. Project Controls Cubed added asset management to the Maximo system to build a digital twin (before the term became prevalent) so all stakeholders could understand, visualize and track their major equipment (and warranties) at operation and maintenance levels for the entire lifecycle of the EchoWater Project.
“This is a live treatment plant that was already producing secondary treatment that we had to shut down—cut over 22 new facilities—to become a tertiary treatment facility,” notes Campbell. “All that needs to be centralized.”
To better understand the engineering scope, there were nine different designers, and each created multiple designs—nearly 100 different designs in total. Each design was delivered to Project Controls Cubed with a construction schedule and cost estimate. All these designs and plans had to be integrated into a single model.
“How do you plan for something that has so many touch points such as construction traffic?” notes Campbell. “How many different designers are there going to be? How many different contractors are going to be working on the same campus? All of that needs to be centralized, and the planning, scheduling and cost control also needed to be centralized.”
Getting Synched
Going beyond a more-traditional 3D model into the 4D and 5D aspects that include costing and scheduling information required newer technology that was just being developed in 2012. Project Controls Cubed had been using Bentley Systems’ SYNCHRO software for such planning, and they ran a test model on one of the earlier EchoWater projects to see if it would be effective.
The Biological Nutrient Removal (BNR) Project is a massive facility at the heart of the EchoWater Project, explains Campbell. “It’s 18 football fields and had a very specific [concrete] pour requirement in their specifications,” he adds. “We used that as one of our first practices to see if the SYNCHRO platform was going to work, and it did.”
“The first time we ran the [SYNCHRO] animation, within the first 30 seconds, we discovered three issues,” notes Greg Sturges, BIM program manager for Brown & Caldwell.
At this point, the EchoWater Project management team was hooked and began using SYNCHRO across the entire project.
“When you can visually see a schedule with the 3D model, you can catch mistakes so much faster than you can going through 3,000 pages of drawings and a contractor’s schedule to try to picture where the problems are,” adds Dan Wilson, program interface manager and senior civil engineer for SacSewer.
Serelle Corn, a licensed architect and managing member at Project Controls Cubed, was impressed by the SacSewer management team’s ability to look past immediate costs and see the big picture. “Most people think bringing on things such as 4D, 5D, and going to that arena means ‘dollar signs,’” she notes. “But SacSewer’s management thought about saving dollar signs [through the entire project], and that’s why I think this team was special.”
Upgrading Through Continuous Operation
Now with support to use SYNCHRO across the project, the model helped plan 22 projects through 11 years to ensure they were sequenced to be brought online at the proper time according to the permits as well as making sure they weren’t stepping over each other in one massive campus that also had to be a continuing treatment plant, which was one of the most difficult aspects of this project.
“Every time a shutdown was necessary while keeping a process online, we would show that in our model, and then we would also run that model by the operation and maintenance staff to make sure they’re onboard and they understand what’s occurring out there in the field,” says Corn. “It was a really good platform for all stakeholders to be able to visualize and have their input.”
“We did a federated commissioning model, where we figured out how we’re going to shut down operational elements of the plant so we could cut them over to tertiary treatment,” adds Campbell. “All of those designers were staggered according to when we needed them, and their designs ‘went on the street’ according to plan.”
“In the design phase—federating all the designs with the schedules—we were able to look at conflicts and site utilization and the potential of site impacts,” adds Kyotani.
“Sometimes there’d be three contractors in one area, and they’re sharing a 6-foot alley, and you need to be very mindful that you don’t put in equipment there,” notes Corn. “That 5D tool was beneficial for everybody to see and study live what’s occurring in the field as well as all the shutdowns and cutovers, the tie-ins, because this is an existing plant, so we need to be able to understand those constraints.”
Making It Mandatory
Adding all the designs, schedules and costs to the SYNCHRO model proved wildly beneficial, but the EchoWater team realized there was still room for improvement. Instead of taking the contractor’s plans and schedules and translating them into the SYNCHRO platform, management realized there were major benefits in requiring contractors to submit their bids in SYNCHRO, eliminating many of the scheduling conflicts upfront and saving additional time and money.
“If the [contractors] run SYNCHRO and see [a conflict], then they will fix it before it ever comes to us,” says Graham Calciano, project advisor at Brown & Caldwell. “It’s giving them another tool to visualize their job.”
The final major project at the EchoWater site, the TTF, was required to be submitted in SYNCHRO, and it was a game changer. “They had the quickest baseline schedule approved, they never fell behind schedule, they made a great profit on their project—even though it was a design-bid-build—and they always caught any of the issues before they provided us their update every single month,” notes Campbell.
“The contractor determined quickly that if they use SYNCHRO to its full capabilities, they can remove every interference issue they might encounter,” adds SacSewer’s Wilson. “We had very little conflicts with the tie-ins and district operation staff interference, because we were able to stay ahead of the contractor [because we had] access to the same SYNCHRO model.”
With major factors such as a rapidly growing population, climate change and increased funding for infrastructure, mega projects will become more common. Hopefully, they’ll use gains in technology to be more like EchoWater and less like the “mega mistakes” found in the past.
“These water-treatment projects coming online today are way too complex to use with technology developed in the 1950s,” notes Campbell. “We need to evolve. We need to use the current generation of technology to make sure we’re delivering these projects on time and on budget.”

About Todd Danielson
Todd Danielson has been in trade technology media for more than 20 years, now the editorial director for V1 Media and all of its publications: Informed Infrastructure, Earth Imaging Journal, Sensors & Systems, Asian Surveying & Mapping, and the video news portal GeoSpatial Stream.